Understanding Factory Laws In India
Factory laws in India primarily aim to regulate the working conditions in factories and ensure the safety, health, and welfare of workers. The cornerstone of these laws is the Factories Act, 1948, which sets comprehensive standards and guidelines for factories.
The Act is enforced by the State Governments, with inspectors appointed to make sure the implementation is done properly. Penalties for non-compliance include fines and imprisonment, depending on the severity of the violation.
The purpose of this article is to provide a comprehensive overview of the regulations governing working conditions and factories in India, offering a deeper understanding of the laws and rules that ensures the safety, health, and welfare of factory workers.
WHAT IS A FACTORY?
A premises where ten or more workers are employed with the aid of power, or twenty or more workers are employed without the aid of power, engaged in manufacturing activities.
- With the aid of power: If a manufacturing premises employs ten or more workers and uses power to operate its machinery or equipment, it falls under the definition of a factory.
- Without the aid of power: If a manufacturing premises employs twenty or more workers but does not use power to operate its machinery or equipment, it is still considered a factory under the Act.
HISTORICAL EVOLUTION
Before the industrial revolution, India’s economy was mostly agriculture based, with artisanal and small-scale industries. There were no formal factory laws as large-scale industrial production was very minimal.
Pre-Independence Era
- The Factories Act, 1881 was the first legislation in India introduced by the British administration, which served towards regulating factory working conditions. It was applied to factories employing 100 or more workers and focused mainly on child labour, limiting the working hours of children and setting minimum age requirements to work in a factory. It also established the system of factory inspections.
- During the course of time, the responsibility of labour legislation was shifted to provincial governments (governments at their state levels), leading to varied implementations.
advertisement
Post-Independence Era
- A more comprehensive legislation was enforced that replaced the earlier Act. It is now called The Factories Act, 1948. It strengthened previous laws and introduced provisions for adult workers, women, and children. Key areas covered included working hours, overtime, holidays, safety, health, welfare amenities, and employment of women and children.
- The act has undergone several amendments over the years to address emerging challenges and align with changing industrial realities. These amendments have focused on issues like hazardous occupations, maternity benefits, sexual harassment, and contract labour.
- Apart from the Factories Act, several other legislations in India were put in place that act as supplementary tools to regulate labour conditions, ensuring the safety, health, and welfare of workers across various sectors. Some of these include:
- Code on Occupational Safety and Working Conditions (OSH), 2020: This code replaced the Factories Act, 1948, and combined the provisions from various other labour laws into one, aiming to provide a more comprehensive understanding of laws for health, safety, and working conditions.
KEY PROVISIONS OF FACTORIES ACT, 1948
The Factories Act, 1948, is a landmark piece of Indian labour legislation designed to safeguard the rights and well-being of workers employed in industrial establishments. It establishes comprehensive regulations governing working hours, safety standards, health conditions, and welfare provisions to create a secure and equitable workplace environment. Some of the important provisions are:
advertisement
Health Provisions: (Sections 11-20)
- Factories must be kept clean and free from waste accumulation, ensuring proper disposal of waste and gases. Adequate measures must be taken to maintain reasonable temperature and ventilation in the work area.
- Sufficient and suitable lighting, both natural and artificial, must be provided. Safe and hygienic drinking water must be made accessible to all workers.
- Adequate and clean latrine and urinal facilities must be provided separately for male and female workers. Effective measures must be taken to prevent the inhalation of dust and fumes and ensure their proper removal.
Safety Provisions: (Sections 21-41)
- All moving parts of machinery and other dangerous parts must be securely fenced/protected to prevent accidents. The fencing should be maintained and kept in position while the machinery is in motion or use. Workers are prohibited from working on or near machinery in motion unless it is essential for the process.
- Young persons (adolescents between 14 and 18 years) are not permitted to work on dangerous machines unless they have been fully instructed regarding the dangers and precautions and have received sufficient training.
- All new machinery installed in a factory must have securely guarded moving parts and other dangerous parts to ensure safety. The term "new machinery" applies to machinery brought into use in any factory after the enforcement of the Factories Act.
- Stairs and lifts must be of good mechanical construction, sound material, and adequate strength. They must be properly maintained and examined at regular intervals. Devices to prevent the fall of the cage or platform and ensure safe operation must be provided.
- No worker shall be required or allowed to lift, carry, or move any load so heavy which is likely to cause injury. Women and children are prohibited from working near cotton-openers (machines of cotton processing) to prevent exposure to dust and other hazards that come during the process.
- Adequate precautions must be taken to prevent workers from being exposed to dangerous fumes, gases, vapours, and dust. This includes providing good ventilation, protective equipment, and ensuring that no worker enters any confined space with dangerous fumes without proper safety measures
advertisement
- Buildings, machinery, and equipment must be of sound construction and properly maintained to ensure safety. Regular inspections and maintenance are required to prevent accidents due to technical failures or machinery failure. Factories employing a specified number of workers must appoint qualified safety officers to oversee and ensure the implementation of safety measures.
Working Hours and Overtime: (Sections 51 and 54)
- Daily and Weekly Working Hours: No adult worker is required or allowed to work in a factory for more than 48 hours in any week. No adult worker is required or allowed to work in a factory for more than 9 hours on any day.
- Rest Intervals: The work shifts for adult workers in a factory should be arranged in such a manner that no shift is longer than five hours. Additionally, no worker should work for more than five hours without taking a break of at least half an hour.
- Weekly Holidays: Every worker should get one day off each week, usually Sunday. If a worker has to work on their day off, they must be given a compensatory day off either within the same month or within the next two months.
- Overtime: If a worker works more than nine hours in a day or more than 48 hours in a week, they must be paid at twice their regular wage rate for the extra hours. Overtime wages should be calculated at twice the normal wage rate, which includes the basic wage and any allowances, but does not include bonuses or overtime wages. (Section 59) clearly states the provision for overtime payment, requiring employers to compensate workers at twice the ordinary wage rate for any hours worked beyond the standard limits.
- Notice of Periods of Work for Adults: A notice must be displayed in every factory showing the periods of work for adults, clearly indicating the time at which each shift begins and ends. Changes in these periods can only be made with due permission from the factory inspector. No adult worker is allowed to work in a factory on any day if they have already worked in another factory on that same day.
advertisement
Employment of Women and Young Persons: (Sections 66-75)
- Restrictions on Employment of Women: Section 66 outlines the restrictions on the working hours and conditions for women, which includes prohibiting their employment during night shifts, which generally means working between 7 PM and 6 AM. However, there are provisions for the government to make exceptions in certain cases.
- Employment of Young Persons: No child who has not completed his fourteenth year shall be required or allowed to work in any factory. A child who has completed his fourteenth year or an adolescent can only be allowed to work in a factory after getting a due fitness certificate from a certified surgeon. This certificate verifies that the young person is fit for employment in a factory. An adolescent having a certificate of fitness is accepted as an adult for the purpose of the working hours and employment conditions.
- Working Hours for Children: Section 71 specifies the working hours and conditions for children (persons below 15 years of age but above 14 years), including restrictions on the number of hours and ensuring adequate intervals for rest. Children are not allowed to work more than 4.5 hours in a day and are prohibited from working during night shifts.
advertisement
Welfare Facilities: (Sections 42-50)
- Washing Facilities: It is mandated that factories must provide and maintain adequate and suitable washing facilities for workers. Factories to provide suitable facilities for storing and drying clothing, especially where workers are required to change their clothes.
- First Aid Facilities: Factories are required to maintain first-aid boxes or cupboards equipped with prescribed contents. These should be readily accessible during all working hours and managed by trained personnel.
- Shelters, Rest Rooms, and Creches: Factories employing more than 150 workers must provide and maintain adequate and suitable shelters, restrooms, and lunchrooms with provisions for drinking water. Also, Section 48 requires factories employing more than 30 women workers to provide and maintain a creche for children under the age of six years of such women. The creche must be adequately staffed, maintained in a clean and sanitary condition, and conveniently accessible for mothers.
- Welfare Officers: Factories employing more than 500 workers, are required to appoint welfare officers to ensure the implementation of welfare provisions. The duties, qualifications, and conditions of service of welfare officers are prescribed by the government.
advertisement
Compliance and Penalties: (Sections 92-106A)
- General Penalty for Offences: If any provision of the Act is violated, the occupier and manager of the factory can be punished with imprisonment up to two years or with a fine up to one lakh rupees, or both. In case the offence continues, an additional fine up to one thousand rupees will be imposed if found convicted.
- Penalty for Obstructing Inspections: If anyone intentionally stops an Inspector to carry out his duties or refuses to produce any document requested by the Inspector, they may be punished with imprisonment up to six months, or with a fine up to ten thousand rupees, or both.
- Penalty for Wrongful disclosures: If someone shares information they learned during an inspection without the factory manager's or owner's permission, they can be punished with up to six months in jail, a fine, or both.
- Penalty for False Certificates: Any person using a false certificate of fitness to get employment in a factory or to allow someone to work, can be punished with imprisonment up to two months, or with a fine up to one thousand rupees, or both.
RECENT AMENDMENTS AND UPDATES IN THE FACTORY LAWS
In recent years, significant amendments have been made to the factory laws in India, primarily to modernize the laws with changing times and improve compliances. Some notable changes that are important to remember are:
- Combination of Multiple Laws: The government has combined 29 different labour laws into four main codes. These codes cover wages, social security, occupational safety and health, and industrial relations. This makes it easier for businesses to understand and comply with the rules. The codes are
- Contract Workers: The rules for hiring and managing contract workers have been updated. The term 'employee' now includes various types of workers like those in IT and call centres. This makes it simpler for businesses to hire and manage these workers without needing many licenses. The Employee's State Insurance Act, 1948 has been amended which covers insurance for long term health issues caused as a result of working shifts in factories. This helps workers get compensation for chronic conditions related to their jobs.
advertisement
- Employee Injuries: The definition of 'employment injury' has been expanded to include diseases that develop over time, like those caused by night shifts or prolonged sitting. This ensures better protection for employees who develop health issues related to their work.
- Simplified Processes: The law now allows for easier changes in work hours, shifts, and moving machinery. It reduces the need for permissions and inspections, making it simpler for businesses to operate without unnecessary delays. Proposed changes have been made in the Factories Act, 1948 for this purpose.
- Increased Benefits: The medical bonus for maternity benefits has been increased, and there's a push to also include paternity benefits. This ensures better support for employees during important life events. For example, the medical bonus for maternity leave has been increased from ₹1,000 to ₹5,000 in large-scale establishments. This provides better financial support to women during maternity leave. Changes have been made to the Maternity Benefits Act, 1961 to support this relief.
IMPACT ON WORKERS AND EMPLOYERS: A CASE STUDY
Factory laws in India and their compliance methods had a diverse impact on both workers and employers, highlighting both the benefits and challenges of these changes. Here are some case studies demonstrating the impact of recent changes to factory laws on workers and employers in India:
advertisement
Impact on IT and Call Centre Workers/Desk Jobs:
- The definition of “employee” has been broadened under the Contract Labour (Regulation & Abolition) Act to include IT and call centre workers. These workers, previously not covered under traditional labour laws, now have greater legal protections. This includes job security, better working conditions, and rights to compensation and benefits.
- Similarly, employers can now simplify their Hiring and Firing policies across different types of workers, making management easy and simple. However, companies faced increased administrative burden to update contracts and policies to comply with the new definitions.
Improved Safety Standards and Self-Certification:
- The Occupational Safety, Health, and Working Conditions Code has allowed companies to self-certify themselves, which means Companies can now declare that they have complied with regulations without needing an external verification from authorities. Workers in factories have reported feeling safer and more secure due to better-maintained working environments and equipment. In a large manufacturing plant in Pune, workers noted a significant decrease in workplace accidents due to more strict safety protocols enforced through self-certification.
Enhanced Maternity Benefits:
- There is an increase in the medical bonus for maternity benefits under the Maternity Benefits Act. Female employees benefit from higher financial support during maternity leave, reducing financial stress and promoting better health for mothers and babies. The amendment increased the duration of paid maternity leave from 12 weeks to 26 weeks for women working in companies with 10 or more employees.
- Additionally, the amendment made it mandatory that employers provide a medical bonus of ₹3,500 if they do not offer free medical care to the pregnant employee. This increase in the medical bonus ensures that women have better financial support during their maternity leave, reducing financial stress and promoting better health for both mothers and their babies. Changes in the Maternity Benefits Act.
- However, higher financial support during maternity leave have increased costs for some businesses, especially small and medium-sized enterprises.
advertisement
Social Security for Gig Workers:
- Social Security for gig workers has been added under the Code on Social Security. Gig workers are those who work temporary jobs typically in the service sector on an independent basis. Gig workers, such as those working for food delivery services, now have access to benefits like health insurance and retirement savings, which were previously unavailable to them.
- In Jaipur, gig workers registered under the new Rajasthan Platform-Based Gig Workers (Registration and Welfare) Act reported feeling more secure in their jobs, knowing they had access to social security benefits. Companies employing gig workers can attract a more stable and reliable workforce by offering social security benefits.
ROLE OF TECHNOLOGY IN EVOLUTION OF FACTORY LAWS
Digital Monitoring:
- The Occupational Safety, Health, and Working Conditions Code encourages digital submissions of safety compliance reports, and files through internet portals reducing administrative delays and corruption.
Automation and Artificial Intelligence (AI):
- Advanced technologies like automation and AI are used to monitor workplace safety. AI-powered systems can detect potential dangers, monitor worker behaviour, and ensure compliance with safety regulations in real-time.
- Factories have implemented AI-driven systems to monitor safety practices and ensure workers are following proper protocols. This has significantly reduced workplace accidents and injuries.
advertisement
Improved Human Resources and Management:
- Combining HR technology with digital systems has made managing labour easier. These systems handle tasks like employee management and ensuring compliance with labour laws, helping factories follow legal requirements more efficiently.
- Companies use HR software to manage employee records, monitor working hours, and ensure compliance with labour laws, including the newly consolidated labour codes.
Enhanced Training and Development:
- Technology has transformed employee training methods. E-learning platforms and Virtual Reality (VR) simulations provide workers with more informative and updated training experiences, ensuring they are well-prepared to handle machinery safely and avoid any damages.
- Manufacturing units have adopted VR-based training systems to educate workers about safety protocols and emergency procedures, enhancing their readiness and reducing the likelihood of accidents.
Remote Inspections and Audits:
- The use of digital tools and platforms for remote inspections and audits has become more useful. This allows government bodies to conduct inspections without being physically present, ensuring compliance even during times of lockdowns, such as during the COVID-19 pandemic.
- The Ministry of Labour and Employment has implemented digital platforms for remote inspections, which helps maintain oversight while minimizing disruption to factory operations.
advertisement
FREQUENTLY ASKED QUESTIONS (FAQs)
1. What are the compliance requirements under the Occupational Safety, Health, and Working Conditions Code, 2020?
The key requirements companies need to follow under this code are:
- Providing a safe working environment.
- Regular health check-ups for employees.
- Ensuring proper safety measures and equipment.
- Adherence to working hour regulations and conditions.
2. How does the self-certification process work for factory compliance?
Factories can now self-certify their compliance with labour laws, submitting necessary documents and reports online. This reduces the need for frequent physical inspections and simplifies the whole process.
3. What are the penalties for non-compliance with factory laws in India?
Penalties for non-compliance can include:
- Fines.
- Imprisonment for severe violations.
- Temporary or permanent closure of the factory.
- Increased surveiallance and inspections by government bodies.
advertisement
4. What are the requirements for maternity benefits under the Maternity Benefits Act, 1961?
The act requires:
- Paid maternity leaves for a specified period.
- Provision of medical bonus and benefits.
- Protection from termination during maternity leave.
- Encouragement for employers to offer paternity benefits as well.
REFERENCES
- Changes and amendments to the factory laws in India
- Enactment of new labour codes
- Important provisions of Factory Act, 1948
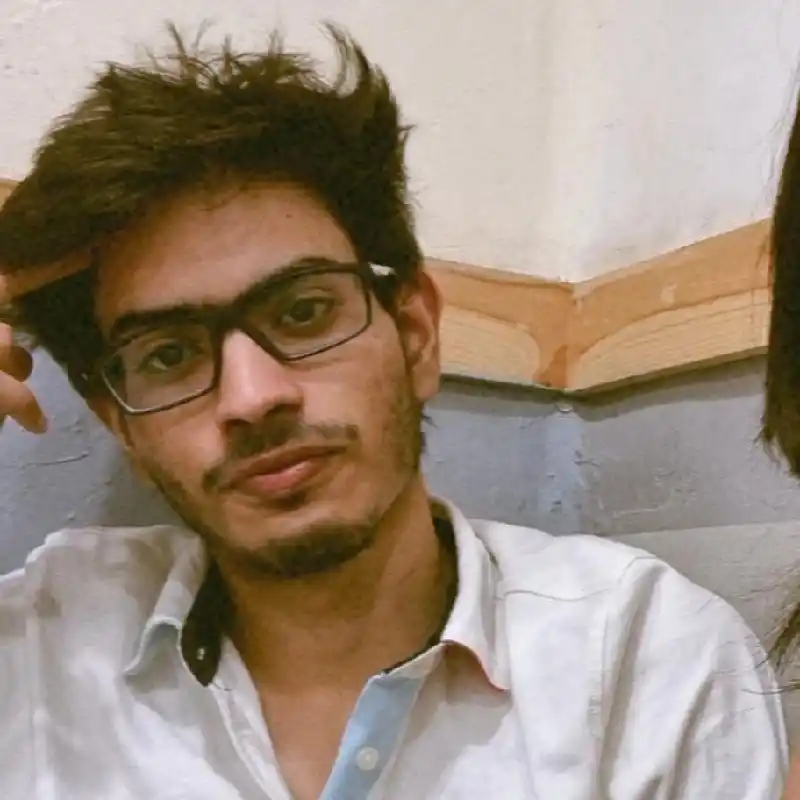
Written by Shubhankar Krishnan
A Delhi University graduate and a 1st Year Law Student, gaining experiences in areas under General Corporate, litigation and Intellectual Property Rights.
advertisement
Further Reading
advertisement